The Role of Structural Insulated Panels in Commercial Roofing
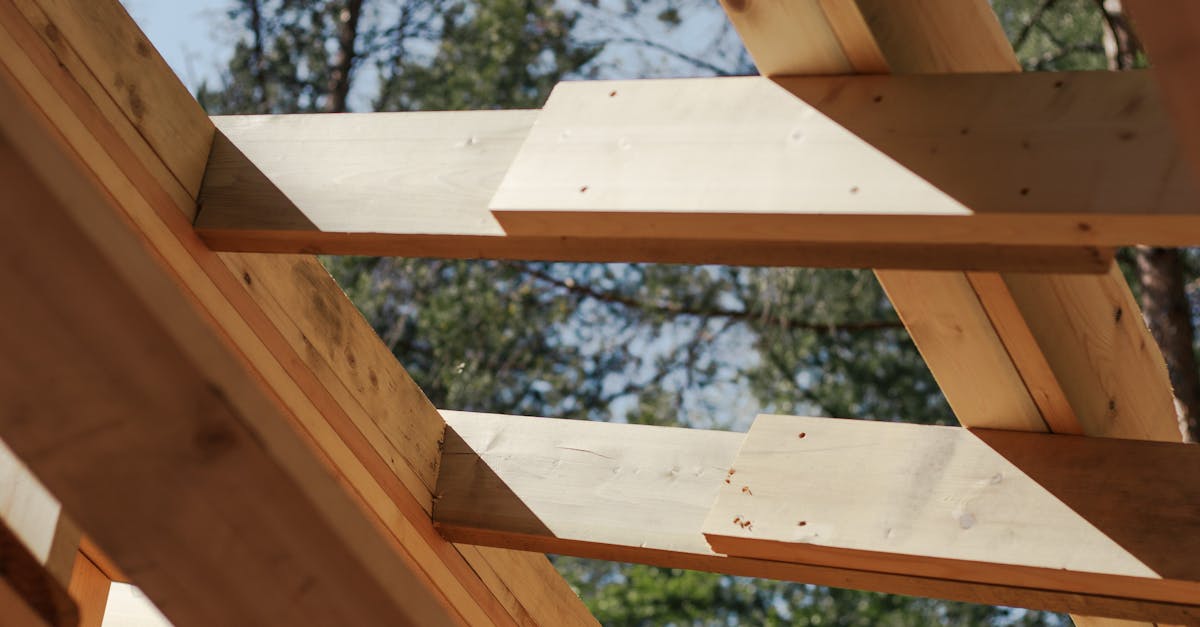
Table Of Contents
Cost Implications of Structural Insulated Panels
Investing in Structural Insulated Panels (SIPs) can initially appear daunting due to the upfront costs associated with this roofing option. The price of SIPs often exceeds traditional roofing materials, which can make decision-makers hesitant. However, considering the long-term financial implications is essential. The energy efficiency afforded by SIPs can lead to significant reductions in heating and cooling expenses. This can help mitigate initial expenditures over time, making them more cost-effective in the long run.
In addition to energy savings, SIPs can also reduce installation time and labour costs. The manufacturing process of SIPs allows for quicker assembly on-site, streamlining construction timelines and potentially leading to fewer on-site labour hours. These efficiencies can result in lower overall project costs, which is particularly appealing for commercial projects with tight budgets. Quantifying these factors is vital for a comprehensive understanding of the financial landscape related to SIPs in commercial roofing.
Long-term Savings vs. Initial Investment
Investing in structural insulated panels (SIPs) for commercial roofing involves a higher initial outlay compared to traditional roofing materials. The upfront expenses can be substantial due to the cost of materials and installation. However, these initial costs should be considered alongside potential long-term benefits. SIPs offer superior insulation properties, which can result in significant energy savings over time. This reduction in energy consumption not only lowers utility bills but also enhances the building’s overall energy efficiency.
The durability of SIPs contributes to their long-term financial advantages. A properly installed SIP roof can last for decades with minimal maintenance, reducing the need for frequent replacements or repairs. This longevity translates to reduced lifecycle costs, as businesses can allocate funds that would have otherwise gone into roof maintenance into other operational areas. By weighing the long-term savings against the initial investment, decision-makers can appreciate the value that structural insulated panels may bring to their commercial roofing projects.
Environmental Impact of Using SIPs
The use of Structural Insulated Panels (SIPs) contributes significantly to reducing the environmental footprint of commercial roofing. These panels offer exceptional insulation properties, which can lead to lower energy consumption for heating and cooling. By enhancing energy efficiency, SIPs help lessens greenhouse gas emissions over time. Additionally, they can be constructed from materials that are sourced sustainably, promoting responsible resource management within the construction industry.
Incorporating SIPs into building designs can also support waste reduction. Their prefabricated nature allows for precise manufacturing, minimising excess material and on-site waste. Utilising SIPs can lead to lighter roofing systems, which often result in reduced structural demands on buildings. This not only conserves resources but also reduces transportation emissions due to lighter loads. Embracing this technology aligns with broader sustainability goals in the commercial construction sector.
Sustainability and Eco-friendliness
Structural Insulated Panels (SIPs) play a significant role in promoting sustainability in the building industry. These panels are designed to provide superior insulation, which can drastically reduce the energy required for heating and cooling commercial buildings. By minimising energy consumption, they directly contribute to a lower carbon footprint compared to traditional roofing systems. Additionally, many SIPs are made from environmentally friendly materials, reinforcing their eco-friendly credentials.
Incorporating SIPs into commercial roofing projects aligns with the growing demand for sustainable construction practices. The use of such panels can also help meet stringent building codes and regulations focused on energy efficiency. As businesses increasingly strive to enhance their green profiles, SIPs offer an effective solution. These panels not only support energy conservation but also encourage the use of recyclable materials, ensuring that the environmental impact of the building process is kept to a minimum.
Maintenance Requirements for SIP Roofs
Structural Insulated Panels (SIPs) are renowned for their durability, yet regular maintenance is essential to ensure their longevity and performance in roofing applications. Inspecting the condition of the panels and their protective membranes periodically can help identify any issues before they escalate. It is also crucial to clear any debris that may accumulate on the roof. Excessive weight or moisture retention can lead to mould growth or structural strain.
The sealing and insulation integrity must be maintained to optimise energy efficiency. It is advisable to check for any signs of wear or damage, particularly around seams and edges. Appropriate repairs should be undertaken promptly to prevent infiltration of water or pests. Implementing these best practices contributes significantly to extending the lifespan of SIP roofs while maximising their benefits in commercial buildings.
Best Practices for Longevity
Ensuring the longevity of SIP roofs starts with proper installation. Engaging certified professionals familiar with SIP systems can significantly influence the roof's durability. Adequate sealing of seams and joints is crucial to prevent moisture ingress, which can lead to long-term damage. Regular inspections after severe weather events can help identify and address potential issues early. This proactive approach is essential in maintaining the structural integrity of the panels over time.
Routine maintenance practices also play a vital role in extending the lifespan of SIP roofs. Keeping gutters clear and ensuring adequate drainage will help prevent water accumulation that could compromise the structure. Additionally, periodic cleaning of the roof surface removes debris that can trap moisture. Addressing minor repairs promptly prevents them from escalating into larger problems. Implementing these best practices promotes not only the safety of the building but also enhances the energy efficiency benefits provided by structural insulated panels.
FAQS
What are Structural Insulated Panels (SIPs) used for in commercial roofing?
Structural Insulated Panels (SIPs) are high-performance building systems that consist of a layer of rigid foam insulation sandwiched between two structural facings, often made of OSB or metal. They provide excellent thermal insulation, strength, and energy efficiency, making them ideal for commercial roofing applications.
How do SIPs contribute to long-term savings in commercial roofing?
While the initial investment for SIPs may be higher than traditional roofing options, they offer significant long-term savings through reduced energy costs, lower heating and cooling demands, and minimal maintenance requirements due to their durability and insulation properties.
Are SIP roofs environmentally friendly?
Yes, SIP roofs are considered environmentally friendly because they are made with sustainable materials and provide superior insulation, which reduces energy consumption and greenhouse gas emissions. Additionally, many SIP manufacturers focus on eco-friendly manufacturing processes.
What are the maintenance requirements for roofs made with SIPs?
SIP roofs typically require minimal maintenance due to their durability and resistance to moisture and pests. Regular inspections for leaks, debris removal, and cleaning can help ensure the longevity of the roof, but overall, they are easier to maintain compared to traditional roofing systems.
What best practices should be followed to ensure the longevity of SIP roofs?
To ensure the longevity of SIP roofs, it's important to conduct regular inspections, promptly address any damage, ensure proper ventilation, and follow manufacturer guidelines for installation and maintenance. Additionally, keeping the roof clear of debris and avoiding excessive weight can help maintain its integrity.
Related Links
Factors to Consider in Choosing Asphalt Shingle Roofing for BusinessesThe Advantages of Metal Roofing in Commercial Settings
Advantages of Thermoplastic Polyolefin Roofing for Commercial Use
Selecting Appropriate Commercial Roofing Materials for Different Climates
Key Features of Modified Bitumen Roofing Systems
Benefits of Green Roof Systems for Commercial Buildings